The second tab on the Stock Item Inventory Window is the Status / Adjustments Tab. Here all relevant quantities, the Total Cost, and all Inventory Transactions for the Stock Item can be reviewed. Further, all Inventory Adjustments for the Stock Item are created and managed on this tab.
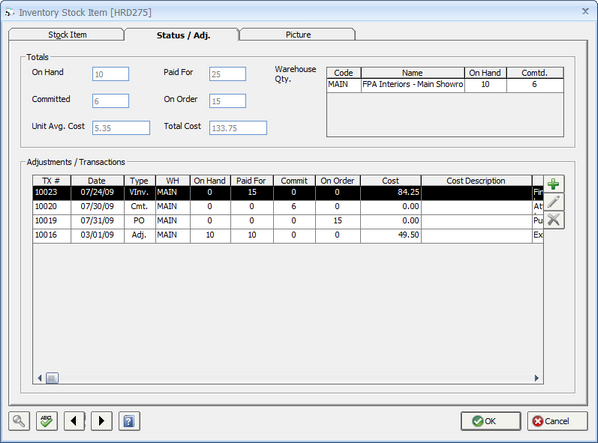
The current quantities and the Total Cost of the Stock Item are displayed in the Totals Frame and are defined below:
On Hand Quantity: The total amount of the Stock Item, across all Warehouses, currently possessed by the company.
Committed Quantity: The total amount of the Stock Item that has been committed to Projects or Orders using the Add Item from Inventory function on the Specifications Window or the From Inventory button on the Component Window.
On Order Quantity: The total amount of the Stock Item currently included on Inventory Purchase Orders but not yet received.
Paid For Quantity: The total amount of the On Hand Quantity for the Stock Item that have been purchased via a Vendor Invoice for an Inventory Purchase Order.
Total Cost: The current total Inventory cost for all units of the Stock Item. The Total Cost is the Stock Items contribution to the company's entire Inventory Cost as displayed on the Inventory List and Inventory List by Warehouse Reports.
Unit Average Cost (Unit Avg. Cost): The Unit Average Cost is the Total Cost divided by the Paid For Quantity. By default, this is the amount that gets transferred from Inventory into Cost of Goods Sold upon invoicing the Stock Item through the Point of Sale system or the Client Invoice window. If no Unit Average Cost is available (i.e., no Total Cost exists for the Stock Item, for example), then the Estimated Unit Cost will be used.
Also within the Totals Frame is the Warehouse Quantity Grid. The Warehouse Quantity Grid displays the Committed and On Hand Quantities of the Stock Item per Warehouse. This grid is a useful tool in quickly determining the amount of the Stock Item in each Warehouse and how much of that amount is already committed to Projects. The sum of those quantities across all the Warehouses will equal the total Committed and On Hand Quantities. Similar information for the Stock Item is available using the Inventory List by Warehouse Report.
Beneath the Totals Grid is the Adjustments / Transactions Grid which lists all Inventory Adjustments recorded for the Stock Item along with any accounting transactions for the Stock Item such as Client or Point of Sale Invoices, Vendor Invoices, etc. The Adjustments / Transactions Grid has the following columns:
• | Transaction Number (TX #): The unique identifier of the Inventory Transaction. |
• | Date: The date of the Inventory Transaction which represents the Invoice Date for Client and Point of Sale Invoices, the Vendor Invoice Date, the date of the Inventory Adjustment, Inventory Purchase Order Date, etc. |
• | Type: The Type represents the classification of the Inventory Transaction and has the following possibilities: |
• | Adjustment (Adj.): A user-entered Inventory Adjustment to manually alter the quantities or Total Cost of the Stock Item. |
• | Committed (Cmt.): The Stock Item was committed to a Project or Order. |
• | Purchase Order (PO): An Inventory Purchase Order was created for the Stock Item. |
• | Received (Rec.): A Received Quantity was recorded for the Stock Item through the Inventory Purchase Order Status Window or the Vendor Invoice Distribution - Inventory Purchase Order Window. |
• | Vendor Invoice (VInv.): A Vendor Invoice was recorded for the Stock Item. |
• | Sale: A Client Invoice for the Stock Item committed to a Project or Order or a Point of Sale Invoice was generated for the Stock Item. |
• | Warehouse Code (WH): The Code of the Warehouse where the Transaction of the Stock Item took place. |
• | On Hand: The affect upon the On Hand Quantity by the Inventory Transaction. A positive value represents an increase on the On Hand while a negative value indicates the On Hand was reduced. |
• | Paid For: The affect upon the Paid For Quantity by the Inventory Transaction. A positive value represents an increase on the Paid For Quantity while a negative value indicates the Paid For was reduced. |
• | Commit: The affect upon the Committed Quantity by the Inventory Transaction. A positive value represents an increase on the Committed Quantity while a negative value indicates the Committed Quantity was reduced. |
• | On Order: The affect upon the On Order Quantity by the Inventory Transaction. A positive value represents an increase on the On Order while a negative value indicates the On Order was reduced. |
• | Cost: The affect upon the Total Cost by the Inventory Transaction. A positive value represents an increase on the Total Cost while a negative value indicates the Total Cost was reduced. |
• | Cost Description: The Cost Description is used to communicate precisely the effect of the Inventory Transaction upon the cost of the Stock Item and is often automatically created by Design Manager. |
• | Transaction Description (TX Description): The Transaction Description for the Inventory Transaction. Many Transaction Descriptions are generated automatically for Inventory Transactions such as "Purchase" for an Inventory Purchase Order being generated for the Stock Item. The Transaction Description for Inventory Adjustments can optionally be entered by the user for future reference. The Inventory Transaction Description appears on many Inventory Reports. |
• | Project Code: For certain Inventory Transactions, such as the Stock Item being Committed to a Project, the Code of the Project will be listed in this column. |
• | Item Number (No.): For certain Inventory Transactions, such as the Stock Item for a Project being invoiced to the Client, the Item Reference Number will be listed in this column. |
• | Component Number (Comp. No.): For certain Inventory Transactions, the Component Number will be listed in this column. |
• | Client Invoice Number (Client Inv. #): For Sale Transactions, when the Stock Item is included on a Client Invoice for a Project or a Point of Sale Invoice, the Invoice Number will be displayed in this column. |
• | Vendor Invoice Transaction Number (VInv. TX #): The Transaction Number for Vendor Invoice Inventory Transactions. |
• | Purchase Order Number (PO #): For certain Inventory Transactions, such as the Stock Item being included on an Inventory Purchase Order, the Inventory Purchase Order Number will be displayed in this column. |
• | Fiscal Month: The Fiscal Month of Vendor Invoice and Sale Inventory Transactions. |
• | Entry Date: The system date and time when the Inventory Transaction was entered into Design Manager. |
Add, Edit, and Delete buttons are available to the right of the Adjustments / Transactions Grid but these are only available to create, revise, and remove Inventory Adjustments for the Stock Item. For more information, see Inventory Adjustments later in this chapter.
|